
MELSEC iQ-F FX5U User’s Manual (Hardware).\nonumber \]Īn example for determining these parameters for a typical process response curve to a step change is shown below. MODBUS Protokolü ve tüm özellikleri nelerdir? The Chinese University of Hong Kong (2019)Ĭonnecting PLCs to Various Software Packages with OPC UA. Smuts, J.F.: Process Control for Practitioners (2011)
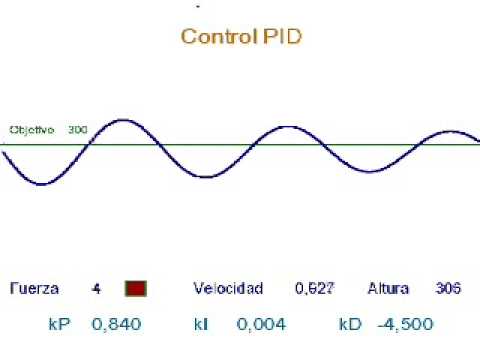
In: Proceedings of MATLAB Conference (2006) Ĭhvostek, T., Foltin, M., Farakas, L.: The adaptive PID controller using OPC toolbox. In: 4th International Conference on Power Engineering, Energy and Electrical Drives, pp. IOP Publishing (2018)īayindir, R., Vadi, S., Goksucukur, F.: Implementation of a PLC and OPC-based DC motor control laboratory.

In: IOP Conference Series: Materials Science and Engineering, vol.

2, 37–45 (2017)įaroqi, A., Ramdhani, M.A., Frasetyio, F., Fadhil, A.: Dc motor speed controller design using pulse width modulation. Hudedmani, M.G., Umayal, R., Kabberalli, S.K., Hittalamani, R.: Programmable logic controller (PLC) in automation. Afyon Kocatepe Üniversitesi Fen ve Mühendislik Bilimleri Dergisi 16, 599–607 (2016) Kutay, M., Ercan, T.: Endüstride Nesnelerin Interneti (IoT) Uygulamaları. Sakarya Üniversitesi Fen Bilimleri Enstitüsü Dergisi 22, 546–556 (2018) KeywordsĪytac, Y.: Endüstri 4.0 ve akıllı fabrikalar.

Also, the conveyor belt system can be monitored in real-time via LabVIEW, the stability of the system can be observed, and fault prediction can be made by processing the speed and encoder data stored via LabVIEW. With the OPC server, reading, writing, and data storage operations can be performed on LabVIEW, and the desired speed value for the PID controller can be adjusted in real-time via LabVIEW. Therefore, PLCs were communicated via MODBUS TCP/IP communication protocol and configured as master-slave, and the OPC server was installed for PLCs, and PLCs were communicated with the LabVIEW program. With these PLCs, the simultaneous interoperability of different PLCs in industrial systems has been demonstrated. Speed control of the conveyor belt is achieved with the help of an Open Platform Communications Unified Architecture (OPC UA) server using multiple Programmable Logic Controllers (PLC) and Proportional-Integral-Derivative (PID) controller algorithm. In this study, it is aimed to control the speed of a conveyor belt system based on the principles of observation, control, data storage and data transfer between systems, which became widespread with Industry 4.0.
